![]()
1 // PRÉSENTATION
Depuis toujours j'ai rêvé de posséder une Super 5 GT Turbo, et dés lors que j'ai eu ma première je n'ai sans cesse cherché à l?améliorer.
Le but d?une préparation est d?augmenter les performances et d?un autre côté de conserver un maximum de fiabilité. J?ai commencé par faire comme tout le monde, modifier le moteur : pression turbo, AAC, carburateur, refroidissement ?, tout en restant dans un budget modeste! Modifier l?allumage était chose quasi impossible mais intéressant afin de récupérer du couple à bas régime perdu suite au montage de l'AAC et limiter le phénomène de cliquetis lors de l'accroissement de la pression en diminuant l'avance en mode turbo. C'est ainsi que j'ai commencé mes recherches sur INTERNET de montages " compatible ". Malheureusement les seules disponibles demandaient de grosses modification (capteur PMH a effet de HALL sur le volant moteur, ...) ou des budgets démesuré : plus de 1200 Euros de modifications.
J?ai donc décidé de fabriquer mon propre module?L?AEI-RE000 pour Super5 GT Turbo, un module PLUG AND PLAY qui se monte en lieu et place de celui d'origine, sans aucune modification du faisceau ou du capteur ...
Ce projet est resté longtemps dans un classeur et dans une partie de ma tête, et à ressurgit de plus belle lors de la rencontre sur le Forum WWW.GT-TURBO.ORGavec McFly Alias Philippe QUILLONqui lui aussi avait créé son propre allumeur pour GTTurbo baptisé AEIP
2 // LE HARD
Le montage est composé d'un micro contrôleur "MAITRE", de la famille MICROCHIP, il doit être capable de stocker 8 Tables de 256 lignes codé sous 8 bits (voir 16 Tables pour une évolution avec un codage sous 16 Bits), intégrer au minimum deux timers (un pour mesurer la vitesse de rotation du moteur et un second pour contrôler la charge de la bobine), mais aussi des convertisseurs Analogique ==> Numérique pour intégrer des capteurs supplémentaires comme : Températures moteur, pression, ... ainsi qu'un UART permettant le dialogue avec un PC au travers du câble RS232
-
Mon choix s'est donc porté sur le PIC 16F876A
- L'ensemble des composants sont installés dans la carcasse d'un module d'allumage d'origine A.E.I Renix - Boitier "F"
- Le module est adapté au capteur PMH en position d'origine, à sa capsule de (dé)pression et à sa bobine HT.
- Le système est paramétrable et ouvert à d'autres fonctions
-
- Mise à jour du microcontrôleur "in situ" (sans le sortir de leurs supports)
- Mise à jour du microcontrôleur "in situ" (sans le sortir de leurs supports)
-
- 1 courbe d'avance "phase suralimentée",
-
- 1 courbe d'avance "phase atmosphérique",
-
- Rupteur/limiteur de régime programmable entre 4900 tr/mn jusqu'à 10 000 tr/mn,
-
- Liaison série RS 232 vers PC, pour programmation (ICSP) sur SUB DB 9 broches et dialogue entre le PC et le module,
-
- Utilisation du logiciel de programmation AEI-COURBE version 2.0,
-
- Gestion témoin au tableau de bord de Shift Light programmable.
- La partie "hard", est complètement différente de l'AEPL de Philippe LOUTREL même si elle à servie de base au raisonnement de cette étude, le module fonctionne avec le capteur de position inductif PMH/PMB monté d'origine sur le véhicule (à la place des vis platinées) et la capsule à (dé)pression. L'architecture électronique a été par conséquent totalement revu et corrigé pour cette nouvelle utilisation !
- La partie "soft", est adaptée au traitement du signal de positionnement villebrequin et donc le programme est spécifique.
- De plus des fonctions supplémentaires ont fait leurs apparitions pour une évolution futur, comme:
-
- Le raccordement d'un capteur de "cliquetis" piézoélectrique, (En cours d'essai)
-
- Des entrées analogiques et numériques comme : températures d'air, d'eau, ... avec seuil paramétrable
-
- Des sorties numériques pour : des voyants, électrovanne d'overboost, ... avec déclanchement réglable
-
- etc...
-
- Ce capteur de position fournit l'image électrique de la cible . C'est un capteur dit à réluctance variable . Il comporte un aimant permanent et une pièce polarisée autour de laquelle est placé un bobinage qui recueille la tension induite à chaque variation de l'entrefer .
- Le circuit de mise en forme est conçu autour d'un "Ampli Opérationel" et d'un microcontrôleur PIC 12C508A OTP (remplacé maintenant par un PIC 12F629 Flash), découplé du capteur et protégé par des diodes.
- Basiquement le capteur détecte les dents du volant moteur, elles sont au nombre de 40 dont deux sont plus larges que les autres et à 180° l'une de l'autre, repérant ainsi le PMH et PMB (mais déphasé de 90° en avance)
- L'amplificateur opérationnel U301 remet en forme le signal issu du capteur à un niveau TTL (0-5 Volts).
- Voici à quoi ressemble le signal en entrée du PIC de gestion du PMH, on se retrouve avec un signal rectangulaire dont deux "CRENEAUX" sont manquant tout les 180° (image du volant moteur)
- Comme vous pouvez le voir sur le schéma ci dessus, suivant le montage du capteur PMH des difficultées de détections sont possible (exemple, si le capteur est mal cablé : fils inversés !!!). En fait, si la gestion se fait sur les fronts montants, les dents manquantes sont vue comme une période double, il y aura des difficultées de reconnaissance du PMH, la meilleur configuration consiste à se placer sur les fronts descendant.
- L'extraction du PMH s'effectue de la façon suivante: on mesure la période du signal et on regarde si elle est au moins deux fois supérieur à la précédente, si oui on à trouvé le PMH, sinon on attend la période suivante
- Ce PMH est ensuite déphasé de 45° ce qui laisse la possibilité de travailler avec les 45° restant.
- Une entrée supplémentaire nommé "CLIQUETIS" est là pour générer un retard de 8° sur la réponse du module si elle est au niveau logique haut.
-
II-1 // HISTORIQUE
TYPON
AEI-RE000
EVO-00(A)
Création des Schémas et Typon sur une seule et même carte
1 - Unité centrale
2 - Entrées, sorties, alimentation et étage de puissance
3 - Gestion du capteur PMH
4 - Gestion du capteur de pression
5 - Gestion du capteur de cliquetis
-
II-2 //ALLUMAGE Electronique Intégral paramétrable pour moteur Renault:
II-3 // Circuit d'adaptation du capteur inductif de PMH:
-
II-4 // Circuit d'adaptation de la bobine d'allumage:
- La résistance de la bobine d'origine est d'environ 0,5 ohms.
- La commutation de la bobine est effectuée par un transistor de puissance de type "Darlington" NPN (ref: S424) monté d'origine dans le module. Celui-ci est conservé en lieu et place sur le boitier afin de lui permettre un bon refroidissement.
- Pour ma part ayant abimé ce TRANSISTOR je l'ai initialement remplacé par la référence BDW83C ayant les caractéristiques suivantes :
Paramètres Valeur Unité Vcb0 100 Volts Vce0 100 Volts Veb0 5 Volts Ic 15 Ampères Ic maxi 40 Ampères Ib 0,5 Ampères P total 130 Watts - Mais ayant eu des problème je l'ai par la suite rapidement remplacé par la référence TIP162 ayant les caractéristiques suivantes :
Paramètres Valeur Unité Vcb0 380 Volts Vce0 380 Volts Veb0 5 Volts Ic 10 Ampères Ic maxi 15 Ampères Ib 1,0 Ampères P total 125 Watts
II-5 // Circuit d'adaptation du détecteur de pressio
- Le détecteur est de type inductif, il se compose d'un solénoïde dans lequel on fait bouger un noyau en ferrite en fonction de la pression présent dans le capteur, faisant ainsi varier son inductance
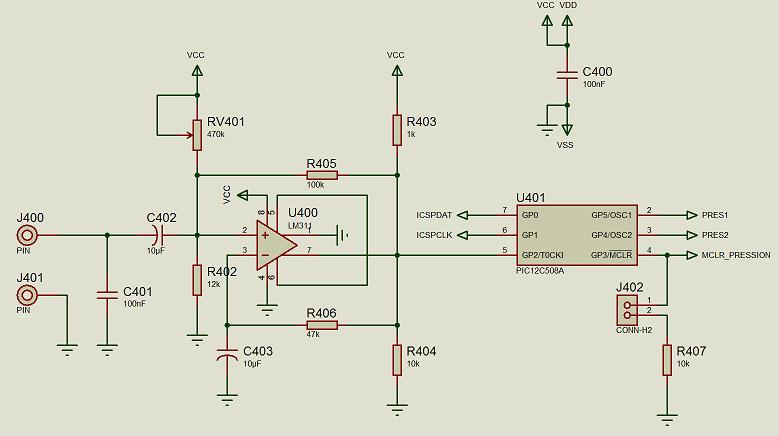
-
-
- L'amplificateur opérationnel U400 sert d'oscillateur, la fréquence varie donc en fonction de l'inductance du capteur dans la plage de : 18 KHz à 32 KHz pour une pression allant de 0 Bar à 1 Bar (et plus) ce qui donne avec la formule
pour un C1 = 100nF l'inductance varie donc entre 732µH et 247µH
-
- Le signal est ensuite envoyé dans un microcontrôleur U401 (PIC 12F629) qui converti cette fréquence en une valeur codé sous 2 bits [00, 01, 10, 11]
PRESSION SORTIES 0 ... 0,2 Bar 00 0,2 ... 0,6 Bar 01 0,6 ... 0,8 Bar 10 0,8 Bar ou plus 11 - Le programme peut être considéré comme un chronomètre qui mesure le temps entre deux impulsions en provenance de l'oscillateur
- Pour le "Chronomètre" j'utilise le TIMER0 du microcontrôleur
- Si Pression = 0 Bar, L(inductance du capteur) sera petite==> Fréquence d'oscillation grande (32 KHz)==> TIMER aura une petite valeur.
- En revanche, si Pression = 1 Bar, L(inductance du capteur) sera grande==> Fréquence d'oscillation petite (13 KHz)==> TIMER aura une plus grande valeur.
- Une nouvelle version est en cours de débuggage avec un mode de calibration automatique des seuils de commutation, ceci afin d'avoir une meilleur réponse du système et une autocalibration du capteur lors du vieillissement de sa membrane
- Le signal est ensuite envoyé dans un microcontrôleur U401 (PIC 12F629) qui converti cette fréquence en une valeur codé sous 2 bits [00, 01, 10, 11]
II-6 // Circuit d'adaptation du détecteur de cliquetis
- Le détecteur est de type piézoélectrique
- Le montage suivant à servit de base pour réaliser l'étage de gestion du capteur de cliquetis présent dans le module de test et son utilisation est en cours de test (Par contre je tiens à emmètre un "bémol" sur ce type de montage qui pour moi n'est pas capable de traiter la détection du cliquetis à lui seul !!!
- L'amplificateur opérationnel U400 sert d'oscillateur, la fréquence varie donc en fonction de l'inductance du capteur dans la plage de : 18 KHz à 32 KHz pour une pression allant de 0 Bar à 1 Bar (et plus) ce qui donne avec la formule
III // Typon
![]() |
![]() |
-
IV // Opérating System
V // LE SOFT
- Pour ce boitier, il faut utiliser le logiciel : AEI-COURBE V2
-
VI // LE CORDON DE COMMUNICATION
Pour la communication entre le module AEI-RE000 et le logiciel AEI-Courbe une simple liaison RS232 est utilisé
utiliser le cordon fourni avec l'AEI lors de l'achat
- Si votre ordinateur n'est pas muni de ce port je vous conseille l'utilisation d'une carte PCMCIA <==> RS232
- Évitez l'utilisation des cordons USB <--> RS232 qui ont un comportement trop aléatoire !!!
-